EV/HEV Sensor SOlutions
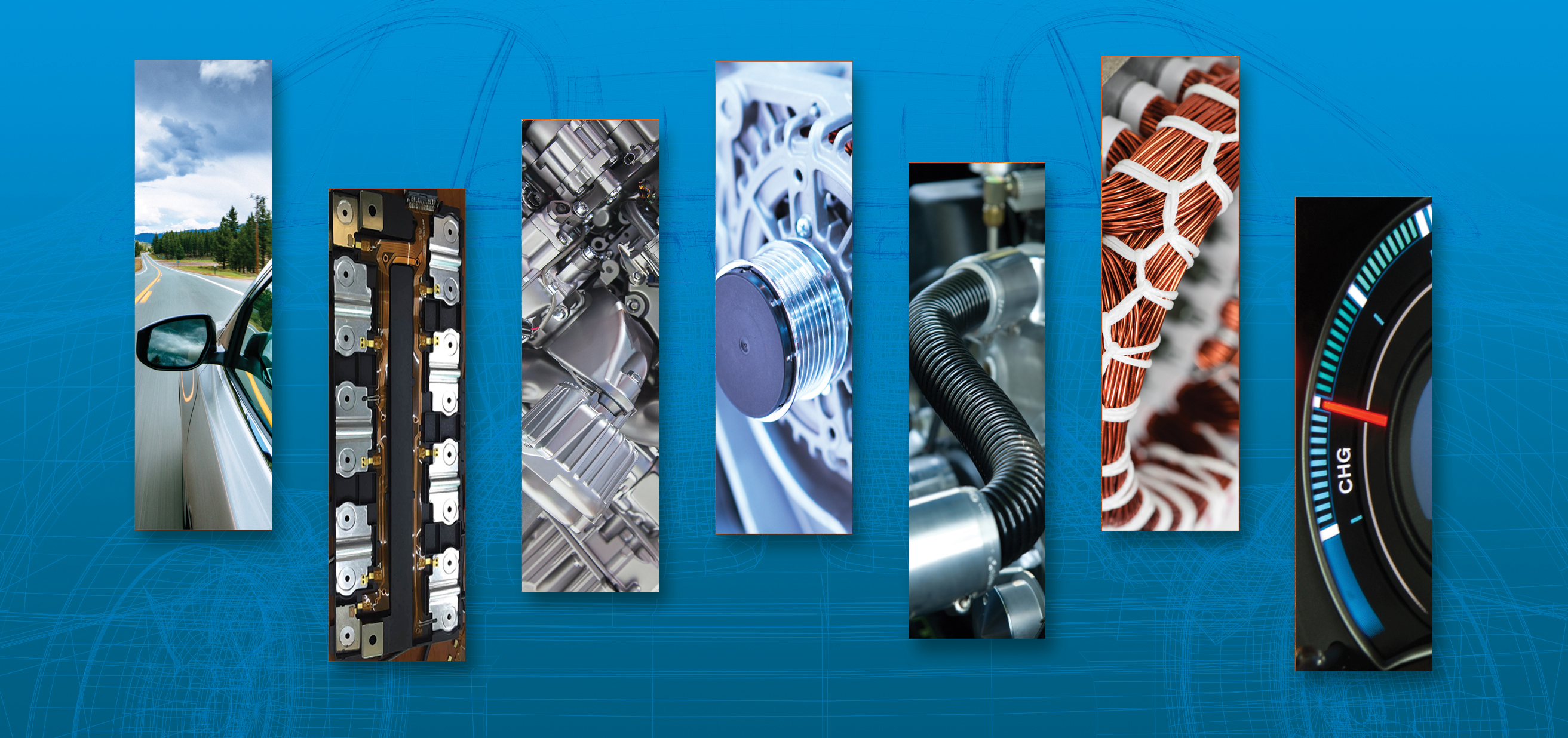
Amphenol Advanced Sensors is a leading innovator in sensor technologies and measurement solutions. Offering the most diverse sensor portfolio of standard and customized products for the world’s most demanding regulatory and industry-driven applications, Amphenol creates value by providing critical information for real-time decisions.
The advantages of Electric and Hybrid Electric Vehicles (EV/HEV) have been long-known. To the everyday driver, they offer reduced fuel costs. For the environment, they utilize renewable energy and offer reduced emissions.
Challenges associated with EV/HEV stem from a limited availability of technologies to enable the use of electricity as a fuel source in a safe and cost-effective manner.
With our vast automotive expertise, engineering resources, and manufacturing capabilities, Amphenol Advanced Sensors offers various EV sensor solutions that enable automotive manufacturers to accelerate the electrification of vehicles around the world.
EV/HEV Sensors By Amphenol Advanced Sensors
Amphenol Advanced Sensors manufactures a wide variety of sensors to optimize EV/HEV performance.
(Click text to jump to section)
Thermal MANAGEMENT ISSUEs
Occurs when battery cells exceed allowable operating temperature causing an explosion/fire, which then propagates, or spreads, to other cells within the battery pack.
Temperature Sensors
|
Pressure Sensors
|
Gas Detection Sensors
|
Battery PAck
Consists of a cluster of individual batteries that serve as the primary fuel source of the vehicle, replacing hydrocarbon fuels used in conventional ICE automobiles.
Temperature Sensors
|
Cell Connection System (CCS)
Used as top cover of the battery cell to provide connectivity with the Battery Management System (BMS).
Temperature Sensors
|
Battery Coolant
Circulates around the battery cell to assist in maintaining optimum battery temperature.
Temperature Sensors
|
Pressure Sensors
|
Ultrasonic Level Sensors
|
Combined Pressure & Temperature Sensors
|
Power Inverter/E-Motor
Converts higher voltage DC electricity to lower voltage AC electricity that is required to power the electric motor.
Temperature Sensors
|
Pressure Sensors
|
Temperature Sensors
|