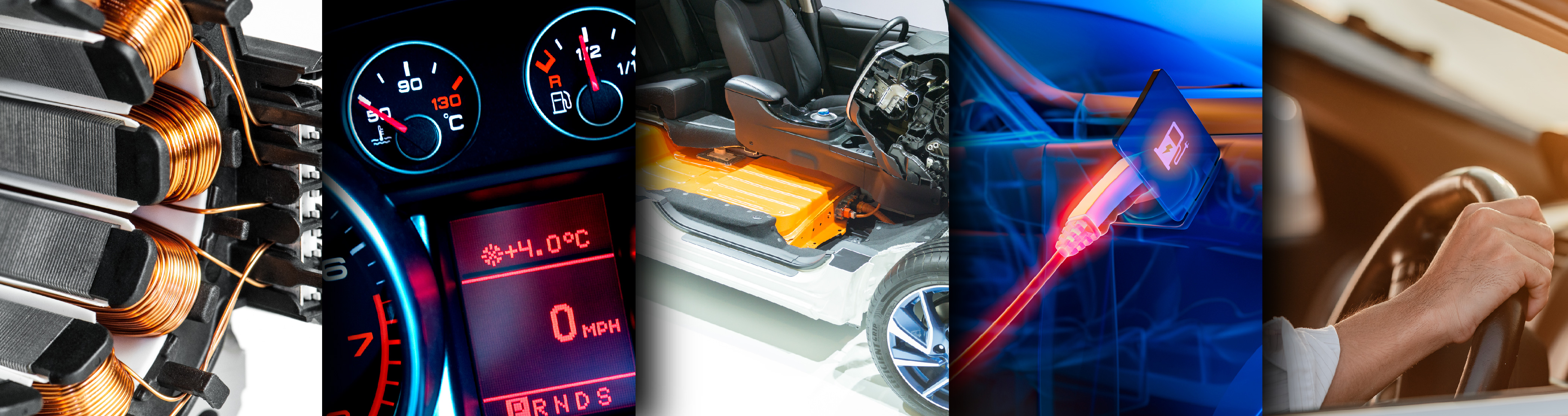
A Manufacturer’s Guide to EV Thermal Management & Sensor Technology
- • How Battery Thermal Management Systems Impact EV Battery Performance
- • Thermal Runaway Prevention, Detection, & Mitigation in EVs
- • Gas Detection for Thermal Runaway in Lithium-Ion Battery Packs
- • Electric Car Battery Pack Design & Sensors for Leak Detection
- • 7 Places for EV Temperature Sensors in Vehicle Design
- • Optimizing Fast Charging With EV Sensors
For as long as there’s been a vehicle propelled by an engine, thermal management has always been a concern.
That’s no surprise – the temperature of an engine, as well as the surrounding components, impact a vehicle’s performance and safety. Outside of normal heat thresholds, the consequences of poor thermal management can be as inconvenient as overheating to as damaging as a fire.
Transportation is in the midst of a revolution. Vehicles of all makes and models are being converted from fossil fuels to electricity.
Though it will be some time before all modes of transportation are electrified, the simple fact is the vehicle of the future is here.
Fully electric vehicles are starting to dominate roadways. They’ll outnumber traditional cars in trucks in a few short years. And in the not-too-distant future, planes, boats, and trains will run off of battery technology, too.
Like their traditional fossil fuel-powered counterparts, thermal management for EVs matters.
Arguably, it’s always mattered more.
Next to a mass charging infrastructure and range, thermal management for EVs – primarily their batteries – was a major hurdle to overcome in making an alternative vehicle type viable. Figuring out the mechanisms to keep the battery and engine temperatures in check meant creating vehicles that could meet consumers’ expectations – having a vehicle that’s ready for a jaunt to the supermarket or a long road trip with friends.
And now that EVs are here, proper thermal management systems ensure the next generation of transportation remains dependable and safe.
Despite its ability to meet the demands of normal and long-term use – something unthought of just two decades ago – EV technology is delicate. It requires a stable, temperature-controlled environment to operate at peak performance and have a long, useful life. What’s more, battery thermal events pose unique safety risks that drivers, passengers, first responders, and automakers have never had to monitor for or contend with – namely, thermal runaway.
For EV manufacturers, fast, accurate, and responsive thermal management systems are an absolute must for vehicle design – from the battery pack to the engine block.
How Battery Thermal Management Systems Impact EV Battery Performance
"As the most expensive part of the vehicle, monitoring an EV’s battery health is critical to maximizing efficiency and performance."
At the core of every electric vehicle is its lithium-ion battery pack.
Without its power, an EV is nothing more than a glorified replica of its traditional counterpart.
Sensor technology strategically integrated into the EV battery pack helps the user monitor the power supply to not only gauge how far their vehicle will take them but also how much life the battery has left. An intelligent battery management system (BMS) can ensure confidence that despite heavy traffic, snowstorms, or other obstacles, a vehicle has enough energy to get to its destination.
While EV battery thermal management systems help manage temperatures and energy flow, sensors help regulate the system itself and provide alerts of potential problems.
Battery Thermal Management Systems & Sensor Intelligence
What’s an EV battery’s worst enemy? Extreme temperatures.
Lithium-ion battery cells perform best in a temperature range between 15-45℃. Temperatures above that are severely damaging to the battery, while colder temperatures reduce the output of the battery’s cells, decreasing range and available power.
Even when an EV isn’t in use (recharging), thermal management systems are always working to monitor or maintain battery internal temperatures. While any temperatures outside the optimal comfort zone will impact EV car efficiency, the vehicle has clever systems to keep the system in its own comfort zone. Generally, when discharging, the batteries prefer to stay below 45℃, and while fast charging, they like temperatures somewhat above that temperature, around 55℃, to reduce the internal impedance of the cells and allow the electrons to quickly fill the cell.
Temperatures Above 45℃ |
Temperatures Below 15℃ |
Excessive heat damages lithium-ion batteries and extreme temperatures, such as those above 60℃, increase the risk to driver and passenger safety. Beyond 45℃, an EV battery’s cells can degrade quickly. This requires that the system be controlled by heat exchangers that can both extract heat from the cells and add heat when the system is too cold. What causes overheating in an EV battery? When cells are actively charging or discharging, they generate internal heat. Most of this heat moves through the metal current collectors and is extracted in the busbar via convection or through the cold plate under the cells through conduction from the cells to the cold plate to the coolant, which then leaves the pack to reject heat through external heat exchangers. Care must be taken when fast-charging, as the cells will generate heat as they are charging. The heat must be absorbed and drawn away from the cells very carefully, as the cells must not exceed their maximum temperature. Sophisticated models in the battery management system determine the best strategy for controlling the heaters and coolant flow. Temperature sensors at the cells and throughout the cooling system are needed to provide real-time data for the model to operate properly. If cells are charged too quickly or overheat while the vehicle is in use, the system must take quick action to immediately reduce the temperature of the cells. If not, heat-induced battery cell degradation can start the process of thermal runaway. Regardless of the heating source, temperature sensors within the EV battery thermal management system play an essential role in detecting excessive heat and engaging mitigating action. |
Thermal management systems aren’t only about keeping an EV battery cool. In cooler climates, the thermal management of electric vehicle battery systems induces heat to keep temperatures above the minimum. They heat the battery before use — whether to power the vehicle, accept power from recharging, or act as a power source. At colder temperatures, the internal kinetics of the cell cause lower charge and discharge rates, reducing available battery power. Cold temperatures slow the chemical and physical reactions that make EV batteries work efficiently. Without intervention, this would increase impedance (resulting in longer charging times) and lower capacity (resulting in range reduction). Forcing too much charge into the cells when they are extremely cold can cause the lithium to form dendrites. These can pierce the separator between the anode and cathode, causing a short circuit inside the cell. Therefore, charge rates are controlled in extremely cold climates to carefully warm the battery, increasing the charge rate only when the battery is above a minimum operating temperature. Internal combustion engine (ICE) vehicles might appear to have an advantage when it comes to cold weather, generating substantial waste heat that keeps vehicles warm in cold temperatures. Without this waste heat, EVs must divert power from batteries to support heating and cooling. However, due to the highly efficient design of the heat pump systems on EV applications, along with heated/cooled seats and other technologies to put heating and cooling only when and where it is needed, they have proven themselves to be much better vehicles to get stuck in a snowstorm or summer traffic jam in than their ICE ancestors. |
EV Sensor Technology for A Long, Optimized Battery Life
Sensor technology placed throughout the battery pack is key to maintaining a battery in both the short and long term. Sensor technology engages the thermal management systems in electric vehicles to start working as soon as temperatures outside the comfort zone range are registered.
Temperatures that are too hot or too cold have similar effects on an EV battery and its health. Excessive temperatures impact EVs in several ways, including:
(Hover over images to learn more)
While the BMS continuously monitors voltage and current entering and leaving the pack, it also controls systems outside the pack to manage temperature, such as the refrigerant and coolant loops.
To manage these systems, the BMS makes use of coolant temperature sensors in and out of the pack’s cold plate as well as cell and busbar temperature inside the pack. This also extends to monitoring coolant temperature at the external heat exchangers, as well as pressure and temperature at the expansion valves and critical points along the refrigerant loop. This high level of monitoring by sensors provides critical data to control precise amounts of heating and cooling from these systems to optimize pack performance while minimizing the parasitic energy loss from running pumps, compressors, and auxiliary heating and cooling components.
Ready to Talk EV Sensor Tech?So are our application engineers. Book time today to discuss your project: |
Preventing Thermal Runaway | Management And Mitigation in EVs
"Though rare, thermal runaway in a lithium-ion battery can result in damage to the vehicle battery pack and the vehicle itself, as well as serious injury to any occupants."
Once considered a barrier for alternative energy vehicles to enter the market en masse, thermal management – or more specifically, thermal runaway prevention – of lithium-ion battery packs remains a key component for the long-term viability of EVs.
What Does a Thermal Runaway Look Like in an Electric Vehicle?
Often triggered by a short circuit, overcharging, or other cell stressors, a thermal runaway occurs when a lithium-ion battery becomes overheated and its cells decompose. The excess heat triggers an uncontrolled chain reaction that spreads throughout the rest of the EV battery pack. As the runaway takes hold and battery cells break down, the runaway causes the release of flammable gases, such as:
- Hydrogen
- Volatile hydrocarbons
- Carbon monoxide
Other hazardous gases released during a thermal runaway include:
- Hydrogen Fluoride
- Carbon dioxide
- Dimethyl carbonate
- Acetonitrile
Once a thermal runaway begins, it’s difficult to stop as its chain reaction can cascade through a battery pack, often causing smoke and flames. With quick intervention, it’s possible to limit a thermal runaway’s impact on a battery pack and the rest of a vehicle. While many materials used in the pack are designed to reduce the risk of fire propagation, once a cell vents gas, a hazardous condition exists within the battery pack that must be identified and dealt with to prevent the risk of fire.
Take a Deeper Dive into Thermal Runaway Prevention & Protection for EVsVisit our Thermal Runaway Resource Hub: |
Battery Management for Thermal Runaway Prevention
Thermal runaway prevention in EVs requires a three-pronged approach:
- Preventing the runaway from starting in the first place
- Identifying if or when a thermal runaway is occurring within a cell
- Stopping the runaway from spreading to other parts of the battery pack
In any case, stopping a battery thermal event happens through two methods -- active and passive thermal management systems.
(Hover over images to learn more)
Gas Detection for Thermal Runaway in Lithium-Ion Battery Packs
Keeping an EV running at peak performance involves constant monitoring of its systems. Regardless of an EV’s thermal management system for its battery pack, sensors play a critical role in stopping a thermal runaway from spreading.
Lithium-ion battery pack thermal management systems initially relied on sensors that measured heat -- the immediate, obvious sign of a thermal battery event. Now, sophisticated sensor technology is taking a much different -- and more scientific -- approach toward thermal management. In addition to heat, BMS systems for the gas release of a venting cell, the precursor to thermal runaway.
Hydrocarbon sensors and air pressure sensors have been trialed to manage thermal runaway, but aren’t accurate or robust means for thermal runaway detection. Other materials inside a battery housing unit can interfere with a chemical sensor’s performance, skewing their readings and ultimately causing the device to fail. Air pressure sensors are vulnerable to variations in the pack’s venting system as well as altitude and temperature changes in the vehicle.
Physics-based gas sensors using technologies such as thermal conductivity or infrared spectroscopy, on the other hand, rely on gas physics to detect the signs of thermal runaway and allow for continuous monitoring after a battery thermal event begins. Using light-based and thermal conductivity technologies, gas sensors measure for CO2 and hydrogen -- the first gases vented by a battery cell during a thermal event. Unlike hydrocarbon and pressure sensors, these sensors are not affected by their environment in ways that degrade their performance over time, and their readings only measure the gases released at the beginning stage of a thermal runaway. These measurements are critical in providing the earliest possible warning to the battery control system, thereby reducing the risk that the thermal event will spread to other batteries in the pack, and providing a best-case scenario for safety and response.
Fluid Sensors for EV Thermal Management
At a macro level, thermal management for EV batteries goes beyond temperature sensors.
In monitoring an electric vehicle’s battery health, leak detection is an absolute necessity whether the vehicle is charging or on the road. Leaks of any sort may directly impact the battery or the systems that keep its temperatures within a suitable range for optimal performance.
The most important leaks to monitor for in an EV’s battery pack are:
Liquid CoolantRather than circulating through an engine block like in an IC engine, coolant is circulated in a closed loop around an electric vehicle’s battery pack, inverter, cabin, and possibly even the motors to keep temperatures within a suitable range of 15-45°C. The thermal management system allows the battery, inverter, and motors to function without overheating and triggering power-limiting mode or shutdown.
Sensors Needed for Detection: Coolant level sensors, coolant breach sensors, and coolant temperature sensors |
RefrigerantWhile all EVs with an air conditioning system use refrigerants to keep the passenger space cool, some manufacturers use the same system to keep battery pack temperatures in check. Using heat pump systems, refrigerant-based battery cooling takes two forms:
|
Dielectric OilA newer battery pack thermal management system with promising applications, dielectric oil cooling boasts superior battery pack temperature control. Inside the battery pack, battery cells are immersed in dielectric oil that’s circulated in a closed loop through the unit. The oil -- an engineered thermal conductive fluid -- not only keeps battery cells cool, but also suppresses thermal events. Sensors Needed for Detection: Oil level/quality/dielectric sensors, oil temperature sensor |
ElectrolytesIn monitoring an electric vehicle’s battery health, measuring the presence of electrolyte leakage is useful in determining if cells within the pack are failing due to age or other stress conditions. These leaks would typically only occur within the battery enclosure and cannot be observed outside the vehicle, so sensors inside the battery pack must be used to detect this event. |
New Technology = New Regulations
As with any new technology used by the masses, new regulations typically follow.
In the case of Li-ion batteries for electric vehicles, new laws and standards are starting to emerge.
The Chinese government regulations for eclectic vehicles are strict guidelines on the inclusion and function of thermal runaway management systems inside electric vehicles. These mandate that any electric vehicle system must be able to provide a warning of a thermal runaway event five minutes before a hazard occurrence in the passenger compartment.
The UN has issued guidelines for similar safety measures in electric vehicles – yet these remain just guidelines. While there are electric vehicle regulations in the U.S., there are no requirements regarding thermal runaway management.
In tandem with laws and regulations, new industry standards are being implemented for thermal runaway detection as EV technology takes hold in transportation.
Performance requirements for thermal runaway management systems are extremely high. For instance:
- • Any thermal runaway event must be detected well before any hazard is posed to the vehicle's inhabitants.
- • A thermal runaway management system must also provide stable operation throughout the entire service life of a battery pack (which can run as high as 10-15 years in automobile applications.)
- • Electric vehicles typically use a 12V secondary battery system to power auxiliary systems such as keyless entry and alarms, which severely limits the power draw of a thermal runaway detection system. A robust thermal runaway detection system ideally needs to have a current draw in the <1 mA range to avoid depleting this secondary battery system.
- • Electric vehicles and energy storage systems commonly use one of several different battery electrochemistries, as well as different cell geometries and configurations. Any thermal runaway detection solution must be agnostic to all of these and provide reliable detection for any battery system.
Beyond the Battery: 6 Places for Electric Car Temperature Sensors in Vehicle Design
Like an ICE vehicle, excessive heat severely impacts an EV’s functionality and safety, as well as its useful life. Arguably, car temperature sensors play a much broader role in an EV, as many of its components are more sensitive to or perform poorly in sub-optimal temperatures.
Beyond the EV battery pack, there are six places where temperature sensors are a must:
- Motor
- Inverter
- Charger handle, port, and high voltage connectors
- Thermal management system
- Passenger cabin
- Under the hood
1. Motor
EV motors are no different from the engines of ICE vehicles -- they have many components working seamlessly together. And more importantly, they get hot when in use.
Like an ICE engine, an EV motor needs to be kept within a certain temperature range to run efficiently -- between 90-95 ℃. Going beyond that range in an EV causes overheating, during which the engine may run inefficiently or enter safe mode.
Install electric vehicle temperature sensors to monitor:
- Electric motor oil temperature
- Electric motor winding temperature
- Electric motor coolant temperature
Electric motor temperature control isn’t strictly about keeping temperatures down. In colder climates, motor temperatures need to be brought up to around 15 ℃ before driving for efficient operation.
2. Inverter
As the channel through which DC energy is converted to AC to power the motor, inverters control the lifeblood of an electric vehicle. A byproduct of that conversion of current is heat, which, when unchecked, can far exceed the temperature limit of 150 ℃. When exposed to excessive heat for too long, the interior components start to fail and the device won’t function properly.
Common effects of overheating on inverters include:
- Insulation degradation
- Solder cracking
- Metal warping
3. Charger Handle & Port
As the source of an EV’s power, the EV charger’s handle and charging port can overheat too. High temperatures are indicative of a few issues:
- Poor connection
- Charger malfunction
Monitoring temperatures of an EV’s charging handle and its port will become increasingly important as fast DC charging technology evolves. Though fast-charge technology has decreased re-energizing times to 30 minutes for 80% power, consumers are seeking a refueling experience similar to filling a gas tank today.
Fast charging requires converting a large amount of power, which generates a large amount of heat. As the technology improves for quicker recharging times, monitoring temperatures helps ensure the process is safe and efficient.
4. Thermal Management System
While the base function of a thermal management system is to regulate an EV’s mechanical components and battery, the system itself needs monitoring too.
A thermal management system’s temperatures directly impact the EV components it’s supposed to cool. When its temperatures spike beyond normal ranges, a domino effect may happen, causing many of the same issues previously listed. Critical information to system controllers to optimize performance and minimize power consumption while maintaining appropriate system temperatures with temperature sensors monitoring critical points in both coolant and refrigerant systems.
High temperatures within a thermal management system are a sure sign that something’s wrong, be it a malfunction inside the system -- such as a leak -- or a failure in one of the components it’s cooling.
5. Passenger Cabin
A vehicle that’s too hot or cold makes for a long, uncomfortable ride. Besides its motor, an electric vehicle’s HVAC system is the next-most noticeable thing running while an EV is on.
The cornerstone of an electric vehicle’s functionality is efficiency -- or making sure it uses no more power than absolutely necessary. Electric vehicle sensors tell the car and computer exactly how hard the vehicle’s systems need to work.
With in-cabin electric vehicle HVAC system temperature sensors, drivers and passengers stay comfortable without draining the battery too quickly and reducing its range.
6. Under the Hood
Exterior temperature sensors aren’t about giving drivers and passengers an idea of the climate they’re stepping into.
Like an in-cabin HVAC temperature sensor, an external device tells the vehicle how hard some of its other systems, such as the thermal management system, have to work to overcome environmental temperatures. Outside temperature sensors are typically installed under the hood of a car or truck.
Explore Our Electric Vehicle SensorsCheck out our sensor technology (plus a host of other resources) for EVs at our EV Sensor Resource Hub: |
Fast Charging & Electric Vehicle Sensors:
A Necessary Pairing
Ask any driver what’s the most important feature of their car or truck, and most will likely say the ability to safely get from point A to point B. That is, after all, the primary function of a vehicle.
The last thing any car owner wants is to find their vehicle isn’t ready when they are. An empty tank of gas won’t get them to that important client meeting or their kid’s soccer tournament. The same goes for a depleted battery.
While electric vehicles use a different fuel source than their traditional combustion engine counterparts, that doesn’t change an owner’s expectation of their vehicle -- or fleet of vehicles -- for immediate, on-demand transportation.
Despite advances in battery technology, there’s still a perception that electric vehicles will run out of power at the worst possible time -- when the driver is miles away from a charging station. What’s more, gas-powered vehicle owners are used to refueling taking only a few minutes. How can charging an electric vehicle ever approach that speed and convenience?
Coupled with longer-lasting power banks, fast-charging EV technology meets these concerns, helping EVs keep pace with cars and trucks running on fossil fuels.
Even still, fast-charging technology and an accompanying infrastructure of charging stations aren’t enough to help potential EV consumers overcome worries about time lost re-energizing. To those looking for a seamless transition to driving an electric vehicle, actual results matter. Electric vehicle sensors are necessary for making charging nearly as quick as fueling up at a gas station.
Fast Charging And Its Potential Impacts on
EV Battery Health
" A missing puzzle piece in the early days of electric vehicle development, new fast-charging technology is responsible in part for the ongoing electrification of transportation. "
While fast-charging systems make the conversion to electric vehicles more practical, they can’t be used without proper monitoring.
Why?
The primary byproduct of fast charging is heat, especially when converting electrical current from AC to DC. Heat is an electric vehicle battery pack’s worst enemy.
3 Places Electric Vehicle Sensors Are Necessary to Monitor Fast Charging
Ensuring that high-speed EV charging is safe and efficient starts and stops with sensor technology. Fast charging requires fast-response sensors -- primarily vehicle temperature sensors.
Without real-time monitoring that triggers the systems that maintain ideal temperatures, the risk of heat damage to an EV’s components increases drastically.
There are three places in an electric vehicle where temperature sensors are a must for fast charging:
- The point of connection
- Thermal management system
- Inside the battery pack
1. The Point of Connection
Temperature sensors are a must in two places at the point of connection: the charging port and the charging handle.
To charge quickly, many electrons need to pass from the EV service equipment to the vehicle battery quickly. This high current generates heat. High temperatures within the charging port may indicate there’s a poor connection between the charging handle and the EV’s contacts. From an efficiency standpoint, a poor connection means the vehicle isn’t charging as quickly as it should be. In addition, high temperatures from an EV quick charger’s connector are also a sign the charger is overtaxed by the power demand, or that it’s starting to malfunction.
2. The Thermal Management System
Overheating within an EV’s thermal management system is an immediate signal that it’s not working as intended and its components are running hot, such as:
- Heat exchangers
- Cooling plates
- Coolant fluids
- Refrigerants
- Dielectric oils
Excessive temperatures are also a sign that the EV cooling system is being overwhelmed by excessive heat from the parts they’re supposed to be cooling.
3. The Battery
Lithium-ion cells charge well when they are between 45 and 60C, but can suffer damage slightly above those temperatures when charging. When in-pack temperatures go beyond that range, the vehicle may go into safe mode and shut down, or worse, start the process of thermal runaway.
A battery overheating is one of the last indicators that something isn’t right with the vehicle’s charging or thermal management systems, or the battery itself is malfunctioning.
To maintain the battery’s long-term functionality and safety, immediate cooling is a necessity.
The Future of EV Fast Charging
The development of fast-charging technology is far from finished.
With existing fast-charging technology, it takes around 30 minutes to re-energize an EV's battery to 80%. However, engineers are still working to make fully charging an EV as fast as filling up an ICE vehicle’s empty gas tank -- a process that typically takes less than 10 minutes.
The demands for ultra-fast electric vehicle charging aren’t entirely driven by the desire for convenience. Ground transit companies and those with fleets of large vehicles (semis and buses) are all but demanding ultra-fast charging, which could have their vehicles mobile within a matter of minutes.
Put simply, larger vehicles have battery packs several times bigger than those used in electric cars. They take longer to charge. But time spent charging represents lost productivity and income.
Fast-response sensors that monitor heat throughout an EV are critical to:
- Putting vehicles back in service faster
- Preventing battery degradation or damage
Electric Vehicle Sensors & Fast-Charging Systems: A Necessary Pairing
Though electrification is one of the biggest transitions in the history of transportation, vehicle owners and operators still have a certain level of expectation for functionality. Fast-charging technology is making this shift possible as it meets a major concern head-on.
Electric vehicle sensors are the unsung heroes in making EV charging as uneventful as filling up a gas tank.
EV Thermal Management | Powering the Electrification Revolution
The literal power behind vehicles is now changing the way we get from point A to point B. To that end, the sensor technology needed to keep vehicles running efficiently and safely must be robust, reliable, and responsive.
These attributes matter the most when it comes to EV thermal management. A natural byproduct of using an EV, unmitigated excessive heat in an electric car, truck, or vehicle of any sort has the potential to derail the electrification revolution. Consumers and consumer protection agencies have great long-term memory when it comes to safety failures or mischaracterized performance.
With the appropriate sensor technology integrated into an EV’s design, EV thermal management is seamless. What’s more, an electric vehicle’s performance is hardly distinguishable from their slowly sunsetting fossil fuel-powered predecessors.
Integrate Amphenol Sensor to Your EV Design
Our industry-leading sensor technology is designed for long-term performance and unparalleled accuracy in EVs. Speak with one of our EV application engineers today: